ISBN 978-85-85905-15-6
Área
Materiais
Autores
Azevedo, L. (IFMA) ; Paiva, A.E. (IFMA)
Resumo
O objetivo deste trabalho foi avaliar a utilização de fibras do epicarpo do coco babaçu em combinação, ou não, com fibras de eucalipto para confecção de painéis de madeiras resinado a frio. As chapas foram prensadas a temperatura ambiente, utilizando-se teor de 25% de resina uréia-formaldeído. As propriedades físicas e mecânicas avaliadas foram: teor de umidade (TU), inchamento em espessura (IE) em 2 h e 24 h, absorção de água (AA) em 2 h e 24 h, densidade e resistência à flexão (RF), de acordo com ABNT NBR 14810-2. Todos os painéis confeccionados obtiveram bom desempenho para os ensaios físicos e mecânicos Portanto, a fibra do epicarpo do coco babaçu apresenta potencial técnico para aplicação em chapas de fibras de madeira curadas a frio
Palavras chaves
Painéis; Úreia-formaldeído; Propriedades
Introdução
Cada vez mais produtos a base de madeira em substituição a outros materiais vem sendo utilizados pela vantagem de ser um material renovável, disponível em grande abundancia, biodegradável ou durável dependendo do tratamento e reciclável.Comparado a outros processos produtivos, a produção de painéis a base de madeira consome bem menos energia do que as indústrias de produção de aços, plásticos e cimentos. A substituição de florestas nativas por florestas plantadas, principalmente dos gêneros pinus e eucalipto, com certo destaque para o primeiro, provocou um aumento expressivo na produção e no consumo de painéis à base de madeira. Entre estes, destaca-se os painéis de MDF (Medium Density Fiberboard), um dos mais avançados tecnologicamente. São formados por processos de prensagem a seco e utilizam como matéria-prima madeira desfibrada termomecânicamente com adição de resina sintética, geralmente a base de uréia-formaldeído.A produção de painéis alternativos, com aproveitamento de resíduos de diferentes origens pode contribuir para o atendimento da demanda de painéis e estimular a produção de novos materiais e de painéis para uso arquitetônico. Adicionado ao fato de que o uso de resíduos lignocelulósicos e plásticos contribui para amenizar os impactos ambientais.Seguindo essa linha, esta pesquisa busca a ampliação dos estudos para a elaboração e produção de painéis de fibras de madeira alternativos com a utilização do epicarpo do babaçu como componente complementar, associado ao eucalipto. Desta forma, o principal objetivo deste trabalho foi testar o potencial de utilização da fibra de eucalipto associado a fibras do epicarpo do babaçu em forma de painéis de madeira, avaliando-se a influencia da granulometria e a interação entre elas nas propriedades físicas e mecânicas dos painéis produzidos e visando o aproveitamento ecologicamente correto dos recursos naturais disponíveis no Brasil, principalmente no estado do Maranhão.
Material e métodos
Foram utilizados cavacos de árvores de Eucalyptus grandis de sete anos, obtidos na fazenda situada no município de Urbano Santos, estado do Maranhão, pertencente às Empresas Suzano Papel e Celulose.Como matéria-prima de adição utilizou-se o epicarpo do coco babaçu, oriundo da Empresa Florestas Brasileiras S.A, situada no município de Itapecuru Mirim, estado do Maranhão. As fibras da casca do coco babaçu (epicarpo) foram obtidas por trituração inicial das cascas na máquina de trituração rotativa da Empresa fornecedora desta matéria-prima. Como material de cola, foi utilizada uma resina a base de uréia-formaldeído, com nome comercial COLAMITE, fabricada pela empresa EUROAMERICAM e comercializada pela empresa LÉO MADEIRAS, fabricantes de painéis MDF. A dosagem de resina utilizada neste trabalho foi de 25% em relação ao total de fibras secas. Para facilitar o processo de desfibramento, os cavacos de eucalipto e as fibras do epicarpo do coco babaçu foram submetidos a um tratamento conforme descrito por Eleotério (2000), cumprindo-se os seguintes procedimentos: a) Imersão em água a 25° C por 72 horas, com troca de água a cada 24 horas; b) Secagem ao ar livre por 48 horas; c) Imersão das fibras em solução de hidróxido de sódio por 72 horas. Após secarem, os cavacos de eucalipto e o epicarpo do babaçu foram imersos em solução de hidróxido de sódio a 10% para facilitar o desfibramento. Após o tratamento, os cavacos do eucalipto e o epicarpo do coco babaçu foram processados em moinho picador de dois martelos fixos e duas facas. Em seguida, as fibras geradas a partir dos cavacos de eucalipto e do epicarpo do coco babaçu foram passadas em um classificador de peneiras, separando-as de acordo com seus tamanhos.A resina e as fibras foram colocadas em um misturador planetário da marca PAVITEST, utilizado para homogeneizar as fibras com a resina. Após a homogeneização, as fibras umedecidas com a cola foram compactadas manualmente, em molde de madeira no formato de uma caixa nas dimensões de 30 x 20 x 15 para a formação do colchão de partículas.Os painéis foram prensados em uma prensa manual da marca SCHWING SIWA equipamentos industriais Ltda, capacidade máxima de 15 t de carga, a temperatura ambiente (a frio), pressão de compactação de 1 MPa e tempo de prensagem de 8 horas por painel. Depois de prensados os painéis foram mantidos à temperatura ambiente, por 24 h para atingirem a umidade de equilíbrio.
Resultado e discussão
As fibras de eucalipto e de coco babaçu foram utilizados na fabricação de painéis de forma pura (100%) ou misturados. A proporção de misturas das fibras, provenientes das duas fibras, foi de 50% e 50% nos painéis com dois tipos de fibras. A resina uréia-formaldeído (UF) foi utilizada na proporção de 25% e a densidade nominal calculada para os painéis foi de 0,80 g/cm³.
A granulometria das fibras geradas a partir das madeiras de eucalipto e do resíduo do epicarpo do babaçu, em condições laboratoriais, é apresentada na Tabela 1.
Os resultados apresentados na Tabela 1 mostram que as fibras de eucalipto proporcionaram partículas de maior granulometria em relação às fibras obtidas do coco babaçu, tendo em vista a maior quantidade de finos gerados no fundo pelas fibras de coco babaçu.
O teor de umidade das diferentes fibras, antes e após a aplicação da resina, está apresentado na Tabela 1.2
Observa-se na Tabela 1.2 que os valores de teor de umidade das partículas antes da aplicação da resina encontram-se acima da faixa do intervalo normalmente utilizado para a produção de painéis. Este intervalo varia entre 3% e 6% de umidade segundo Moslemi (1974). Entretanto, estes valores foram reduzidos após o processo de secagem a valores próximos aos recomendados na literatura, conforme mostrado na tabela 1.2.
A Tabela 1.3 mostra a densidade básica dos cavacos de eucalipto e do coco babaçu antes da etapa de aplicação da resina.
Os teores médios e o coeficiente de variação (CV) de umidade dos painéis, após o período de climatização, são apresentados na Tabela 1.4.
Conforme observado nos resultados da Tabela 1.4 o teor de umidade para todas as formulações avaliadas atendem aos requisitos da Norma Brasileira ABNT NBR 15316-2 e consequentemente a sua correspondente Norma Européia EN 622-5, que delimitam o teor de umidade mínima de 4% e a máxima de 11%.
Os valores médios das propriedades de absorção de água e inchamento em espessura após 2 horas e 24 horas de imersão em água estão apresentados na Tabela 1.5.
Os resultados de absorção de água demonstram que a fibra de coco babaçu influenciou na redução da absorção de água, conforme menores valores de absorção de água dos painéis confeccionados com a mistura das fibras, em relação aos painéis contendo somente fibra de eucalipto (quando comparados painéis com a mesma granulometria. A granulometria também influenciou na absorção de água dos painéis contendo somente fibras de eucalipto e também nas formulações contendo fibras de coco babaçu.
Em relação às propriedades mecânicas, a tabela 1.6 apresenta os resultados médios para o Módulo de Ruptura (MOR) obtido a partir dos ensaios mecânicos em flexão estática.
Comparando os valores médios da Tabela 1.6 com trabalhos publicados por outros pesquisadores, exemplo, Brito et al. (2004) em trabalho com painéis de madeira aglomerada, produzidos com resíduos de serraria (serragem e maravalha) de madeira de Pinus elliottii, encontrou valores entre 9,74 a 13,58 MPa para MOR.
O resultado final da aglutinação das Fibras de Coco Babacu e Eucalipto é apresentado na Figura 1 abaixo.
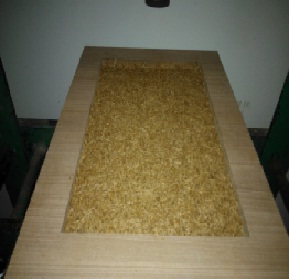
Resultado final da aglutinação das Fibras de Coco Babacu e Eucalipto
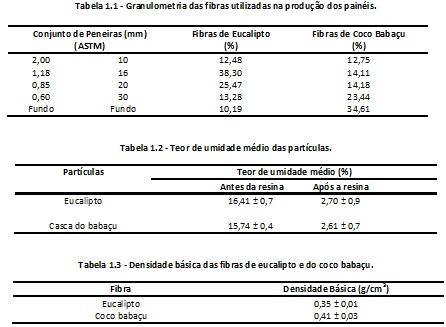
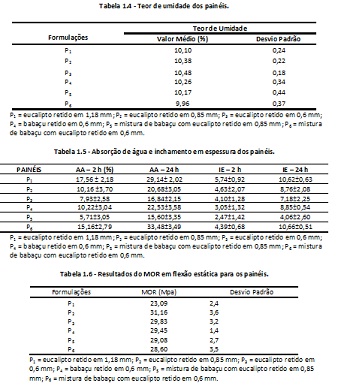
Conclusões
Os valores de Inchamento em espessura em 2h obtidos no presente trabalho estão na faixa de 2% a 6%. Esses valores estão abaixo do valor mínimo especificado pela norma NBR 14810-2. Comparando-se os valores de inchamento em espessura deste trabalho com os das normas e com os encontrados pelos pesquisadores citados, considera-se que os painéis de eucalipto, painéis de epicarpo do babaçu, ou painéis com 50% de eucalipto e 50% do epicarpo do babaçu apresentaram um bom desempenho.Os valores obtidos de Resistência a Flexão estão na faixa de 23 MPa e 31,16 Mpa, valores estes bem acima ao especificado pela norma NBR 14810-2 (10MPa a 18MPa) e a NBR 15316 (20 Mpa). A fibra do epicarpo do coco babaçu apresenta potencial técnico para aplicação em chapas de fibras de madeira curadas a frio.
Agradecimentos
Ao IFMA, Empresas Suzano Papel e Celulose e Empresa Florestas Brasileiras S.A.
Referências
1. ASSOCIAÇÃO BRASILEIRA DE NORMAS TÉCNICAS – ABNT. NBR 15316-2: Chapas de fibras de média densidade. Parte 2: Requisitos. Rio de janeiro, 2006.
2. ASSOCIAÇÃO BRASILEIRA DE NORMAS TÉCNICAS – ABNT. NBR 14810. Define os termos usualmente empregados na fabricação, comercialização, execução de ensaios e utilização de chapas de madeira aglomerada e seus derivados. Rio de Janeiro: ABNT, 2006.
3. BRITO, Edvá Oliveira et al. Propriedades de chapas produzidas com resíduos do fruto de coco e partículas de pinus. Floresta e Ambiente. v. 11, n. 2, p. 1-6, ago./dez. 2004.
4. ELEOTÉRIO, J. R. Propriedades físicas e mecânicas de painéis MDF de diferentes densidades e teores de resina. 2000. 120f. Dissertação (Mestrado em Engenharia Florestal) – Escola Superior de Agricultura “Luiz de Queiroz”, Piracicaba, 2000.
5. MOSLEMI, A. A. Particleboard. Illinois: Southern Illinois University Press, 1974. v. 1. 244 p.