INFLUÊNCIA DA UMIDADE NO PODER CALORÍFICO DE CAROÇOS DE AÇAÍ
ISBN 978-85-85905-23-1
Área
Produtos Naturais
Autores
Costa, R.L.T. (UFPA) ; Nascimento, R.A. (UFPA) ; Araújo, R.C.S. (UFPA) ; Santana, E.B. (UFPA) ; Azevedo, C.A. (UFPA) ; Andrade, E.L. (UFPA) ; Faria, L.J.G. (UFPA)
Resumo
Para o desenvolvimento desta pesquisa realizaram-se secagens nas temperaturas de 70, 80, 90 e 105°C (sólido seco) para variação da umidade em caroços de açaí (Euterpe oleracea Mart.). Utilizando-se a análise de regressão não linear, constatou-se que o modelo matemático proposto por Midilli et al. (2002) descreveu satisfatoriamente a cinética de secagem dos caroços, com base nas estatísticas: coeficiente de determinação, erro médio relativo e amplitude de resíduos. Para caroços com diferentes umidades, foram obtidos valores de poder calorimétrico superior na faixa de 13,3 a 22,4 MJ/kg e poder calorimétrico inferior entre 11,8 e 21,1 MJ/kg.
Palavras chaves
Secagem; Biomassa; Poder Calorífico
Introdução
A região amazônica, por apresentar um clima favorável, é portadora de variedades de biomassa vegetal. No Estado do Pará, por exemplo, o caroço é o rejeito da produção da bebida do fruto açaí (Euterpe oleracea Mart.), a qual é grandemente popular na região. Atualmente, existem cerca de dez mil pontos de venda de açaí na região metropolitana de Belém, os quais, individualmente, geram em média 200 kg de caroços diariamente (Governo do Estado do Pará, 2017). Uma das aplicações desse resíduo é como combustível para geração de vapor, diminuindo a produção de lixo orgânico no Estado e a perda do aproveitamento energético que pode oferecer. Logo, diante da significativa utilização de biomassas vegetais e da abundância do caroço de açaí no Estado do Pará, é necessário investigar os parâmetros que circundam a utilização dessa matéria-prima disponível, motivando o desenvolvimento deste trabalho.
Material e métodos
Os caroços de açaí foram coletados em Belém, Estado do Pará, e foram lavados para remoção da borra. Para a realização do processo de secagem, utilizou-se um secador de bandejas Quimis Q316M. A secagem foi realizada em duplicata para as temperaturas de 70, 80 e 90°C, até que o teor de umidade de equilíbrio fosse atingido O teor de umidade inicial foi obtido por meio da secagem em estufa a temperatura de 105°C (± 1°C), durante 24 horas. Os dados obtidos experimentalmente, foram avaliados por seis modelos matemáticos, utilizando-se uma análise de regressão não linear, com o auxílio do software Statistica 7.0. Os modelos estão apresentados na Tabela 1, na qual, Xr é razão de umidade do material (adimensional); t é o tempo de secagem (min); K, K1, K2 e K3 são coeficientes de secagem; a, b, c, d e n são constantes dos modelos cinéticos. A escolha do modelo cinético mais adequado foi realizada com base nos parâmetros estatísticos: coeficiente de determinação (R²), erro médio relativo (EMR), calculado pela Equação EMR= (100/N)∑(|Y-Y'|/Y), sendo, Y o valor observado experimentalmente e Y’ o valor predito, além da análise da amplitude dos resíduos. As análises calorimétricas foram baseadas na norma da ASTM D4809 – 13 e realizados para as amostras secas a 70, 80, 90°C e a de sólido seco (105°C). Para a obtenção do poder calorífico superior (PCS), fez-se uso da bomba calorífica manual PARR 6200 CALORIMETER. Para o cálculo do poder calorífico inferior (PCI), Rendeiro et al. (2008) sugere a utilização da Equação PCI=(1-Xbu)×PCSu [9×H×(1-Xbu)×hv-(Xbu×hv)], onde PCSu é o poder calorífico superior da massa úmida, H é o percentual de hidrogênio da amostra, igual a 6% e hv a entalpia de vaporização da água (25°C) igual 2243 KJ/Kg.
Resultado e discussão
Na Tabela 2 são apresentados os valores dos parâmetros estatísticos dos
modelos avaliados. O modelo de Midilli et al. mostrou-se o mais coerente
pois apresentou R² próximo de 1, EMR baixo em comparação aos demais, além
de intervalos de amplitude de resíduos pequenos, ratificando uma mínima
diferença entre o modelo e os pontos experimentais. Na Tabela 3 estão
expressos os parâmetros obtidos pelo modelo de Midilli et al. (2002),
também como na Figura 1, as curvas de secagem geradas a partir do mesmo
modelo, para as temperaturas diferentes temperaturas. A umidade inicial dos
caroços foi de 73% b.s. Para as temperaturas de 70, 80 e 90°C, os teores de
umidade de equilíbrio atingido foi de 5.3% b.s. em 640 minutos; 4,5%, em 550
minutos e 2,6%, em 520 minutos, respectivamente. Portanto, ratificando
Strumillo e Kudra (1986), os quais afirmam que quanto maior a temperatura,
maior a taxa de remoção de umidade e, consequentemente, menor o tempo que se
atinge o teor de umidade de equilíbrio, definindo-se um menor tempo para o
processo. Os valores dos teores de umidade em base úmida (Xbu) e de PCS,
obtidos experimentalmente, e PCI calculados para as diferentes temperaturas,
estão expressos na Tabela 4. Observa-se na Tabela 4 que, quanto maior o teor
de umidade, menor o poder calorífico, conforme Rendeiro et al. (2008)
ratifica, explicando que a umidade é a maior influenciadora do poder
calorífico da biomassa. Quanto maior o teor de água contido no material,
maior será o dispêndio de energia para iniciar o processo de conversão
térmica, em vista de que a energia estará sendo requerida para vaporização
da água e não para as reações do processo.
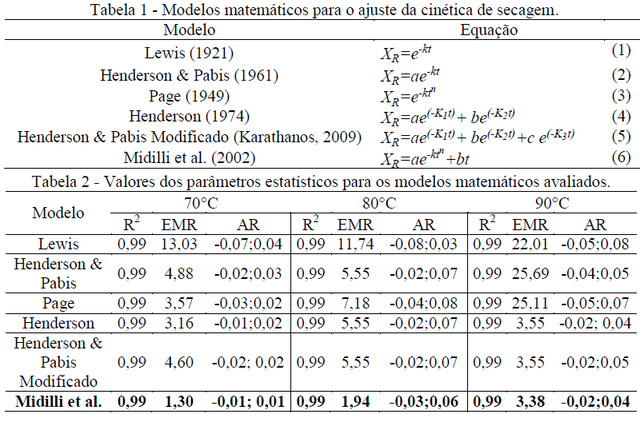
Tabela 1 e Tabela 2.
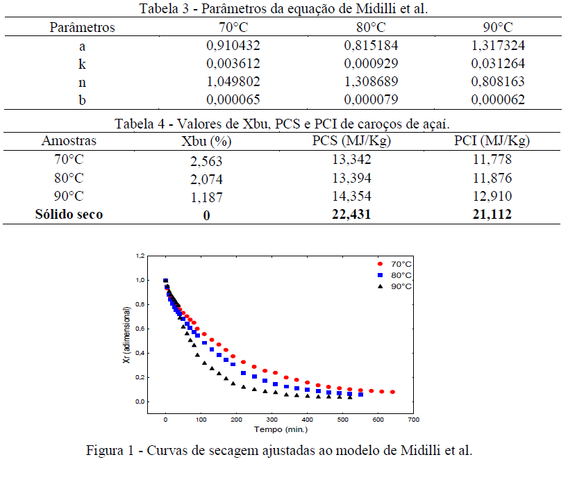
Tabela 3, Tabela 4 e Figura 1.
Conclusões
Pode-se observar que o poder calorífico da biomassa do caroço de açaí sofre influência direta do teor de umidade contido no mesmo. Assim, para a otimização do processo de termoconversão do resíduo, o maior rendimento apresenta-se na utilização do biocombustível totalmente livre de umidade. O modelo matemático predito em relação à secagem do caroço do açaí considerado mais representativo para o processo foi o de Midilli et al. (2002), pois resultou, para as diferentes temperaturas, em um maior valor do coeficiente de determinação(R²), menor erro médio relativo e menor amplitude de resíduos.
Agradecimentos
Referências
GOVERNO DO ESTADO DO PARÁ. 2017. Caroços de açaí. Disponível em: http://para2030.com.br/caroco-de-acai-pode-virar-fonte-de-energia. Acesso em dezembro de 2017.
HENDERSON, S. M. Progress in developing the thin-layer drying equation. Transactions of the ASAE 17, p. 1167-1168/1172, 1974.
HENDERSON, S. M.; PABIS, S. Grain drying theory I. Temperature effect on drying coefficient. Journal of Agriculture Engineering Research, v. 6, n. 3, p. 169-174, 1961.
KHARATANOS, V. T. Determination of water content of dried fruits by drying kinectics. Journal of Food Engineering, vol. 39, n. 2, p. 337-344, 1999.
LEWIS, W. K. The rate of drying of solid materials. The Journal of Industrial and Engineering Chemistry, v. 13, n. 5, p. 427-432, 1921.
MIDILLI, A.; KUCUK, H.; YAPAAR, Z.A. A new model for single-layer drying. Dring Technology, v. 20, n.7, p. 1503-1513, 2002.
PAGE, G. E. Factors influencing the maximum rates of air drying shelled corn in thin layers. 1949. Thesis (M. Sc.) - Purdue University, West Lafayette, 1949.
RENDEIRO, G.; NOGUEIRA, M. F. M.; BRASIL, A. C. M.; CRUZ, D. O. A.; GUERRA, D. R. S.; MACEDO, E. N.; ICHIHARA, J. A. Combustão e Gasificação de Biomassa Sólida. 1. ed. Brasília: Ministério de Minas e Energia, v. 1. 190 p., 2008.
STRUMILLO, C.; KUDRA, T. Drying: principles, applications and design. New York: Gordon and Breach Science Publishers. 448 p. 1986.