OBTENÇÃO E CARACTERIZAÇÃO DE AÇO RÁPIDO OBTIDO POR METALURGIA DO PÓ
ISBN 978-85-85905-25-5
Área
Materiais
Autores
Peixoto, P.H.A. (UNIVERSIDADE FEDERAL RURAL DO SEMIÁRIDO) ; Silva Junior, M.Q. (UNIVERSIDADE FEDERAL RURAL DO SEMIÁRIDO - UFERSA) ; Pereira, K.R.A. (UNIVERSIDADE FEDERAL RURAL DO SEMIÁRIDO - UFERSA) ; Saldanha, R.D.A. (UNIVERSIDADE FEDERAL RURAL DO SEMIÁRIDO - UFERSA) ; Leite, R.H.L. (UNIVERSIDADE FEDERAL RURAL DO SEMIÁRIDO - UFERSA) ; Gonçalves, F.C.P. (UNIVERSIDADE FEDERAL RURAL DO SEMIÁRIDO - UFERSA)
Resumo
O estudo visa obter um aço rápido, através da metalurgia do pó, sem a presença de cobalto (Co), utilizando a composição convencional do mesmo com variação de pressão de compactação e temperatura de sinterização em 09 diferentes amostras. A análise de suas características microestruturais foi realizada através de microscopia ótica e propriedades mecânicas de microdureza. As amostras foram fabricadas com base nos elementos: Ferro (Fe), Molibdênio (Mo), Cromo (Cr), Carbono (C) e Nióbio (Nb) para o Aço Rápido M10, com substituição do Vanádio (V). As amostras apresentaram um baixo coalescimento dos grãos à medida que a temperatura se eleva, aumentando a porosidade do mesmo e acarretando um baixo valor de microdureza em comparação com o mesmo aço produzido por processo convencional.
Palavras chaves
Aço rápido; Metalurgia do pó; Sinterização
Introdução
Há muito tempo foi percebido a dificuldade de produzir peças e elementos para máquinas em geral, para isso foi desenvolvido o processo de usinagem que permite obter peças com dimensionamento preciso e superfície extremamente regular, melhorando a precisão e eficiência dela. (SILVA, 2010). O primeiro grande impacto significativo causado nos materiais para ferramenta de corte aconteceu em meados de 1899, quando Taylor e White desenvolveram o aço rápido (HSS). O aço rápido revolucionou a usinagem da época dando um aumento considerável na produtividade. As velocidades de corte puderam ser ampliadas de 3 a 5 m/min com ferramentas de aço carbono para 30 a 35 m/min com os aços rápidos. (MORO; AURAS, 2007). Uma das formas de obter ferramentas de corte para usinagem é pela mistura e compactação de pós metálicos, denominada de metalurgia do pó, processo este que se desenvolveu mais rapidamente após a Segunda Guerra Mundial para atender a grande demanda no florescente setor automobilístico. (CHIAVERINI, 2001) As principais etapas do processo são: obtenção dos pós, sua mistura, a compressão da mistura resultante com o emprego de matrizes e a sinterização (operação de aquecimento, realizada em condições controladas de temperatura, tempo e atmosfera) através do aquecimento da compactação resultante de modo a produzir uma ligação entre as partículas e conferir resistência mecânica ao material compactado. As partículas são unidas em uma peça única, coesa, similar ao que seria obtido pela fundição dos mesmos materiais juntos. (KALPAKJIAN, 2000). A introdução dessa técnica para produção de aços rápidos surgiu na busca por melhores propriedades utilizando os mesmos materiais, como ligas de tungstênio, cromo, molibdênio, vanádio e cobalto que apresentam baixa solubilidade. Tendo a liga de carboneto de tungstênio (wc) com cobalto (co) uma dificuldade de obtenção pois este último elemento é encontrado em regiões de conflito e por isso há uma alta variação de preço (ARAÚJO FILHO, 2006). A motivação desse estudo é obter uma liga de aço rápido, através de metalurgia do pó, utilizando a composição clássica, ou seja, a mesma composição presente na norma NBR-116-1, já que para o processo de metalurgia do pó, comumente se compacta diretamente os carbonetos. Uma vez obtida a liga por esse método, caracterizá-la por microscopia ótica e ensaio de microdureza.
Material e métodos
Para fabricação do aço, foram adquiridos em forma de pó, os elementos Ferro, Cromo, Molibdênio, Carbono (em forma de grafite) e o Nióbio. O elemento que substituiu o vanádio foi o nióbio, isso devido conferir propriedades físicas semelhantes. Os elementos foram separados na proporção conforme a NBR-116-1, com o auxílio de uma balança de precisão com resolução de 0,0001g. Após a etapa de pesagem de todo o pó, o mesmo foi misturado durante 4 horas contínuas em um recipiente plástico a uma rotação de 30 rpm com auxílio de um torno mecânico da marca Nardini, modelo Nodus 220. Após esse procedimento, o material foi novamente separado com o auxílio da balança de precisão em 09 amostras de 2 g cada. Em seguida, as amostras foram levadas para serem compactadas em uma prensa hidráulica manual, à uma taxa de compressão de 0,5 Ton/10 segundos, até atingir a pressão desejada, em uma matriz de aço 4340, usinada e temperada. As amostras foram distribuídas de modo que 03 fossem compactadas com pressão de 382,2 MPa (3 toneladas), outras 03 com pressão de 509,6 MPa (4 toneladas) e por fim 03 com pressão de compactação de 637 MPa (5 toneladas). Com os compactados verdes produzidos, foram separadas 1 amostra de cada tipo para que fossem sinterizadas em 03 temperaturas diferentes, formando grupos com 03 amostras cada. Após distribuídas as amostras, os grupos foram sinterizados nas temperaturas de 900°C, 1000°C e 1100°C em forno elétrico tipo Mufla, com capacidade de até 1200°C, por um período de 2 horas e resfriamento lento, a taxa de 73°C/h, dentro do próprio forno. Posteriormente foram feitas análises de microscopia ótica e ensaio de microdureza a fim de caracterizar o material e depois compará-lo com o aço rápido forjado. Para que se fosse realizada a microscopia ótica, foi realizado um ensaio de metalografia. O ensaio de microdureza foi efetuado no microdurômetro da Shimadzu, modelo HMV2. Em observância a norma ASTM E384. Os valores colhidos foram tratados no software Microsoft Office Excel® a fim de obter as médias e desvios-padrão.
Resultado e discussão
A microscopia óptica foi realizada com o intuito de se obter fotografias das
microestruturas das amostras e foram realizadas em um aumento de 500x.
Percebe-se por elas a presença de porosidade, que é típica deste processo e
é determinada por diversos fatores, por exemplo os que foram utilizados como
variáveis neste trabalho: a pressão de compactação e a temperatura de
sinterização. Na Figura 1 é possível observar as amostram divididas por
grupos de 3 cada, separadas pela fator da pressão de compactação em ordem
crescente.
Pelas micrografias presentes na Figura 1 Microestrutura das amostras
compactadas a 382,2 MPa. a) 900°C; b) 1000°C; c) 1100°C, amostras 1, 2 e 3,
observa-se um bom coalescimento dos grãos e diminuição da porosidade em
função da temperatura de sinterização, apresentando maior uniformidade na
distribuição dos grãos à medida que a temperatura aumenta.
Já na figura 01 Microestrutura das amostras compactadas a 509,6 MPa. a)
900°C; b) 1000°C; c) 1100°C, amostras 4, 5 e 6, é possível perceber que
houve uma piora no nível de porosidade à medida que a temperatura de
sinterização aumentava. Essas amostras apresentaram, micro estruturalmente,
uma quantidade superior de defeitos, observados nas partes mais escuras.
Esses defeitos possivelmente são causados pela aplicação de temperaturas que
não estão na faixa convencional de sinterização e pelo não controle da
atmosfera durante a sinterização delas.
E observando as imagens da figura 01 Microestrutura das amostras compactadas
a 637 MPa. a) 900°C; b) 1000°C; c) 1100°C, é possível ver que as amostras 7,
8 e 9 apresentam também uma aumento bastante significativo da porosidade à
medida que a temperatura aumenta, indicando mais uma vez uma fraca
coalescência dos grãos em virtude da temperatura de sinterização.
Na Figura 02 a) Valores médios de microdureza (HV) e desvio padrão de cada
amostra, observa-se os valores médios de microdureza e seu respectivo desvio
padrão e a Figura 02 b) Gráfico Microdureza (HV) x Pressão de Compactação
(MPa) é possível observar o gráfico que sintetiza os dados da figura 02 a).
Confrontando a figura 02 a) e b) é possível perceber que houve um aumento na
microdureza das amostras à medida que se eleva a pressão de compactação e a
temperatura de sinterização, porém ao analisar esses resultados com relação
à literatura têm -se que o valor de dureza para o AISI M10, juntamente com a
conversão de HRC para HV, segundo Taylor Special Steels (2018), são valores
baixos em relação aos aproximadamente 860 HV, valor de dureza deste aço a
temperatura ambiente (22°C). Corroborando com Silva (2010) que obteve
valores para os aços rápidos em uma faixa de 740 – 980 HV, já devidamente
convertido.
O fator determinante para que esses resultados fossem baixos foi a
temperatura de sinterização. Como Soares (1993) falou, a temperatura ao qual
os aços rápidos devem ser submetidos para uma sinterização, deve estar na
faixa de 1250 °C a 1350°C, pois segundo ele, abaixo dela, os carbonetos
perdem dureza rapidamente.
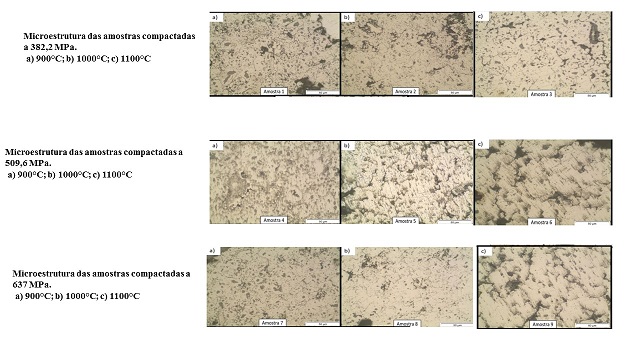
Microestrutura das amostras compactadas à 382,2 MPa ,509,6 MPa e 637 MPa. a) 900°C; b) 1000°C; c) 1100°C.
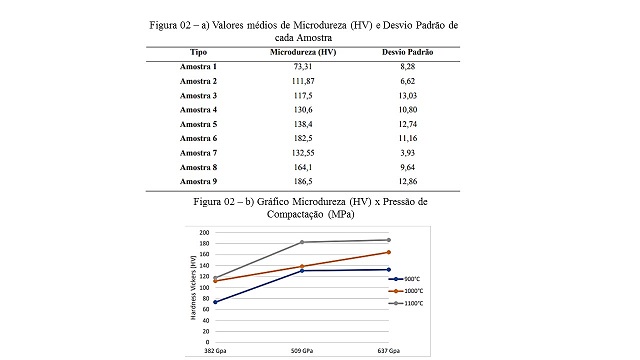
a) Valores médios de microdureza (HV) e desvio padrão de cada amostra, observa-se os valores médios de microdureza e seu respectivo desvio padrão.
Conclusões
A realização desse trabalho possibilitou a obtenção de amostras de aços por metalurgia do pó e a realização dos testes para que se caracterizasse o mesmo. Com base em todos os dados obtidos experimentalmente, é indiscutível que, pelas micrografias, que as amostras produzidas possuem um aumento na porosidade em função da sua temperatura de sinterização, pois os grãos não se unem de forma homogênea. As informações dos ensaios de microdureza apontam a significativa influência de que a temperatura e pressão de compactação interferem no valor da final da dureza do material, porém como não se utilizou a temperatura convencional de sinterização, os grãos não coalesceram uniformemente, resultando nos valores que foram apresentados.
Agradecimentos
Os autores agradecem à Universidade Federal Rural do Semiárido - UFERSA, ao Programa de Pós-Graduação em Ciência e Engenharia dos Materiais, pelo apoio e suporte.
Referências
AMERICAN SOCIETY FOR TESTING AND MATERIALS. E384 - 17: Standard Test Method for Microindentation Hardness of Materials. West Conshohocken, Pensilvânia, Eua, 2017.
ARAUJO FILHO, Oscar Olímpio de. Estudo comparativo de aços rápidos AISI M3:2 produzindo por diferentes processos de fabricação. 2006. 167 f. Tese (Doutorado) - Curso de Tecnologia Nuclear - Materiais, Instituto de Pesquisas Energéticas e Nucleares, São Paulo, 2006.
ASSOCIAÇÃO BRASILEIRA DE NORMAS TÉCNICAS. NBR 116-1: Aços-rápido - Parte 1: Classificação, designação e composição química. Rio de Janeiro - RJ, 2005.
CHIAVERINI, V. Metalurgia do Pó. 4. ed. São Paulo: Associação Brasileira de Metalurgia e Materiais, 2001. 325 p.
KALPAKJIAN, S., Manufacturing Engineering & Tecnology, 4th ed, Addison Wesley, 2000.
MORO, Noberto; AURAS, André Paegles. Metalurgia do Pó e o Futuro da Industria. Florianópolis: Nobertocefetcs, 2007. 27 slides, color.
SILVA, André Luiz V. da Costa e; MEI, Paulo Roberto. Aços e Ligas Especiais. 3. ed. São Paulo: Blucher, 2010. 646 p. 41
SOARES, S. R. S. Desenvolvimento de ligas de Aço Rápido pelo processo de Metalurgia do pó. 1993. 96 f. Dissertação (Mestrado) - Curso de Programa de Pós-graduação em Engenharia Metalúrgica e dos Materiais, Escola de Engenharia, Universidade Federal do Rio Grande do Sul, Porto Alegre, 1993.
Taylor Special Steels. Conversion Chart of Vickers Hardness (HV) to Rockwell C (HRC). Disponível em <http://www.taylorspecialsteels.co.uk/pages/main/conchart.htm> acesso em 17 de abril de 2018.