AVALIAÇÃO DA ALTURA DO LEITO DE SINTERIZAÇÃO EM UM REATOR VERTICAL DE LEITO FIXO PARA A PRODUÇÃO DE SÍNTER
ISBN 978-85-85905-23-1
Área
Materiais
Autores
Neves, A.S.S. (UFPA) ; Daniel, B.T.F. (UFPA) ; Silva, R.N.J.F. (UFPA)
Resumo
O presente trabalho visa a realização do processo de sinterização de finos de minério de ferro, moinha de carvão vegetal e adições, em três alturas, de um Reator Vertical de Leito Fixo e analisar os parâmetros do processo, bem como o desempenho do equipamento e a qualidade dos sínteres produzidos. Deste modo, os produtos obtidos foram caracterizados através de análises em DRX, MEV/EDS, FRX e submetido a testes de tamboreamento. Ao final pode-se afirmar que a melhor altura alcançada no leito de sinterização, dentre os três estudos aqui realizados, o Sínter 2, com a altura de 45 cm, obteve-se resultados satisfatórios, em temperaturas reais de sinterização e consequentemente gerando sínteres com boa qualidade para uma produção em planta piloto.
Palavras chaves
Sínter; Sinterização; Fino de minério de ferro
Introdução
A sinterização do minério de ferro é um processo de agrupamento de partículas minerais que possui como produto resultante uma massa porosa chamada sínter. Embora o sínter apresente granulometria mais grossa e homogênea do que as partículas de sínter feed, sua redutibilidade e resistência mecânica reforçam os benefícios de utilização deste produto como carga metálica do alto-forno para a produção de ferro gusa. As matérias primas utilizadas na composição da mistura de sinterização são: finos de minério de ferro (sínter feed), combustíveis sólidos, fundentes e resíduos siderúrgicos (STARLING, 2012). Em seguida, as partículas vão sendo aglomeradas a frio mediante o acréscimo de água à mistura composta. Os agregados formados ficam sujeitos a um processo de queima em que o ponto de fusão é parcialmente atingido. O processo de sinterização e a qualidade do sínter obtido são diretamente influenciados pela composição da mistura de sinterização. Para Geerdes et al., (2007), as vantagens da aplicação do processo de sinterização levam a maioria das usinas mundiais a operarem com carga de sínter em seus altos-fornos superior a 60%. Neste contexto a larga utilização do sínter nos processos de fabricação de aço justifica o foco que será dado neste trabalho ao processo de aglomeração por sinterização de finos de minério de ferro - FMF, moinha de carvão vegetal - MCV (resíduos gerados durante a produção de ferro gusa) e fino de calcário calcítico - FCC, visto que a etapa de sinterização exerce importância no controle ambiental por ser a maior consumidora de rejeitos gerados nos processos de produção de usinas siderúrgicas, em que os rejeitos retornam como matéria prima no processo de sinterização.
Material e métodos
Para a realização dos experimentos, utilizou-se: aparelho de aquisição de dados de temperatura; reator de leito fixo; maçarico; motor exaustor; termopares; betoneira; peneiras granulométricas; balança analítica; matérias-primas (FMF, MVC, FCC) e estufa com recirculação de ar. Para a metodologia, iniciou-se com o pré-tratamento das matérias- primas com o quarteamento e as caracterizações físico-químicas, e estas foram secas a 105º C na estufa durante 24 h e medidas suas massas secas, além de possuírem granulometrias distribuídas em peneiras de malhas 6,35 mm a 0,53 mm. Realizou-se o método de teor de umidade ótima que determina a quantidade de água necessária para formar as micropelotas e consequentemente a menor densidade aparente. A pesagem das matérias-primas e suas quantidades exatas que seriam sinterizadas em relação às três alturas (55 cm, 45 cm e 35 cm) foram realizadas em uma balança analítica, calculou-se o volume de carga para entrar no reator conforme as alturas, através do volume total pela massa específica, 1,3 g/cm³. A porcentagem para as matérias-primas foi de 70% de FMF, 20% de MCV e 10% de FCC. Para os experimentos usou-se 8.040 kg em relação à altura de 35 cm (Sínter 1), 10.300 kg em relação à altura de 45 cm (Sínter 2) e 12.600 kg em relação à altura de 55 cm (Sínter 3). E as matérias-primas foram micropelotizadas com 10% de H2O em relação as suas massas e abastecidas no sinterizador, para por seguinte iniciar o processo de sinterização. Os sínteres produzidos foram caracterizados através de MEV/EDS, FRX, DRX e teste de tamboreamento, que visa a resistência à abrasão do sínter.
Resultado e discussão
O equipamento conseguiu atingir as expectativas e funcionou corretamente
para a produção dos três experimentos. O Sínter 1 e Sínter 3 apresentaram
fragilidade e não houve uma boa sinterização e resultou em grande quantidade
finos, diferente do Sínter 2. Para a granulometria dos constituintes evitou-
se partículas superfinas, pois prejudicam a permeabilidade do leito e
partículas supergrossas, pois diminuem a resistência do sínter formado. Para
o teste de teor de umidade ótima, optou-se por utilizar 10%, visto que o
valor se encontra dentro dos parâmetros baseado nas literaturas. As
temperaturas dos experimentos foram parecidas em relação ao valor máximo,
ficando entre 1468,7 ºC a 1789,45ºC. Para caracterizar os sínteres, pelo
MEV, notou-se que o Sínter 2 exibiu formas irregulares, partículas mistas,
regiões de nucleação e grande incidência de poros, quando comparados aos
demais experimentos. O EDS exibiu os elementos encontrados nas amostras,
usando como referência o Sínter 2, com teor de cálcio, oxigênio, carbono e o
de ferro na região analisada. Pelo DRX, obtiveram-se as fases cristalinas
predominantes, nas matérias-primas nota-se a presença de: hematita (Fe2O3),
magnetita (Fe3O4), quartzo (SiO2), calcita (CaCO3), dolomita (CaMg(CO3)2) e
caulinita (Al2(SiO5)(OH)4), nos sínteres, nota-se a presença de: hematita
(Fe2O3), magnetita (Fe3O4), cálcio-ferrita (Ca2Fe2O5) e wustita (FeO). Por
FRX observou-se a presença dos óxidos majoritários em comum nos Sínteres 1,
2 e 3 sendo os CaO, silicatos, Al2O3 e o Fe2O3. A resistência ao
tamboreamento entre os sínteres produzidos foi de 45,5% para o sínter 1,
57,4% para o sínter 2 e 41,9% para o sínter 3, onde destaca-se que a melhor
resistência para o teste foi o Sínter 2, pois garantiu pouca geração de
finos em relação aos outros.
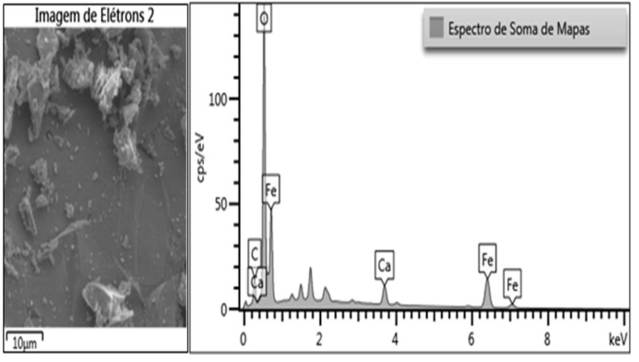
Análise de MEV em uma amostra retirada do meio do bolo de sínter e com os devidos elementos da amostra apresentados por EDS.
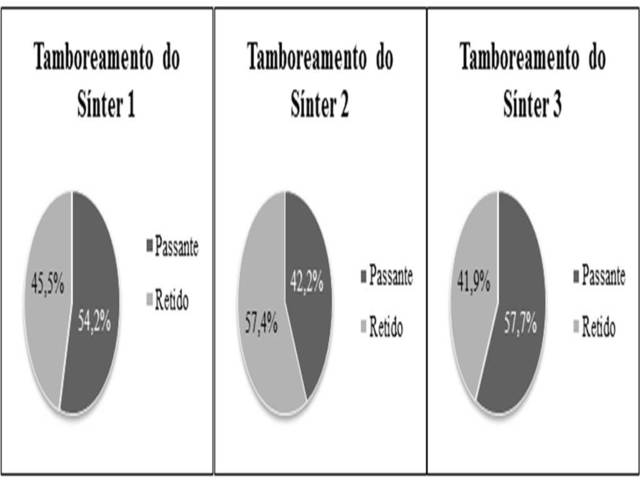
Análise do teste de tamboreamento realizados nos produtos com 1kg de amostra cada.
Conclusões
O reator vertical de leito fixo mostrou-se eficaz no processo de sinterização para obter o sínter de fino de minério de ferro, com boa granulometria e elevadas temperatura reais acima de 1.000 ºC em todos os experimentos, garantindo a eficiência do processo. Os resultados obtidos revelaram que o Sínter 2 com a altura de 45 cm, apresentou grau de sinterização maior, ótima resistência a abrasão, boa granulometria, ótimo rendimento, boa porosidade, alcançou as temperaturas adequadas no processo, características químicas dentro do esperado e aparência física com boa aglomeração.
Agradecimentos
Agradecemos ao Laboratório de Eng. Química - UFPA e a SINOBRAS/PA pelo fornecimento das matérias-primas, pelo auxílio e apoio para o desenvolvimento desta pesquisa.
Referências
ABNT – ASSOCIAÇÃO BRASILEIRA DE NORMAS TÉCNICAS, 2009, “NBR ISO 4701: Minérios de ferro e pré-reduzidos - Determinação da distribuição granulométrica por peneiramento”, Rio de Janeiro.
ABNT – ASSOCIAÇÃO BRASILEIRA DE NORMAS TÉCNICAS, 2011, “NBR ISO 3082: Minérios de ferro - Procedimentos de amostragem e preparação de amostras”, Rio de Janeiro.
ABNT – ASSOCIAÇÃO BRASILEIRA DE NORMAS TÉCNICAS, 2018, “NBR ISO 3271: Minérios de ferro como insumo para alto-forno e redução direta — determinação dos índices de tamboreamento e abrasão”, Rio de Janeiro.
ARAUJO, L. A. Manual de Siderurgia. São Paulo: Arte e Ciência, 1997. v. 1.
CAMPOS, A. R.; FONSECA, V. O. Centro de Tecnologia Mineral - Parte II: pelotização. Rio de Janeiro, Cap. 16, p. 683-750. 2010.
DAWSON, P. R. Part 2 - Research studies on sintering and sinter quality. Ironmaking and Steelmaking, v. 20, n.2, p. 137-143, 1993.
GEERDES, M., TOXOPEUS, H., VLIET, C. V. D. Modern blast furnace ironmaking - an introduction. New York: Ijmuiden, 2004.
GEERDES, M. et al.; Livro: Práticas Modernas para Operação de Alto-Fornos. Coordenação da edição Brasileira. p. 17- 28, 2007.
STARLING, A. R. D. A. R. Avaliação de metodologias de simulação física. 162 f. Dissertação (Mestrado) - Universidade Federal de Minas Gerais. Belo Horizonte, 2012.
DEDAVID, B.A.; GOMES, C.I.; MACHADO, G. Microscopia eletrônica de varredura: aplicações e preparação de amostras: materiais poliméricos, metálicos e semicondutores. Porto Alegre: EDIPUCRS, 2007.
FONTES, A. V. Caracterização Tecnológica de Minério de Ferro Especularítico. – Rio de Janeiro: Escola Politécnica, 2013.
LOPES, M. V. Caracterização do sínter para uso em altos-fornos a carvão vegetal. 2012. 80 f. Dissertação (Mestrado) – Programa de Pós-graduação em Engenharia de Materiais, Itajubá, 2012, p. 14-25.
MARTINS, M.F.; SALVADOR, S.; THOVERT, J.F., DEBENEST, G. Co-current
combustion of oil shale – Parte 2: structure of the combustion front. France: Université de Toulouse, 2010.
QUARESMA, D. S. Estudo da Sinterização em Reator Vertical de Leito Fixo: Desenvolvimento de Processo para Produção de Agregado Sintético a Partir de Cinza Volante e Biomassa. Tese de Doutorado – PRODERNA. Universidade Federal do Pará, 2016, p. 159.
TAKANO, C. Estudo da influência de alguns combustíveis na sinterização de minério de ferro. 1970. 110 f. Tese (Doutorado) – Escola Politécnica, Universidade de São Paulo, São Paulo, 1970.