ESTUDO DA PRODUÇÃO DE ACETATO DE METILA: SIMULAÇÃO DE PROCESSO E AVALIAÇÃO ECONÔMICA DE UMA UNIDADE INDUSTRIAL
ISBN 978-85-85905-23-1
Área
Química Tecnológica
Autores
Silva Neto, F.C. (UFERSA) ; de Albuquerque Júnior, E.B. (UFERSA) ; Mendes Costa, R. (UFERSA) ; Fonseca de Lima, Q. (UFERSA) ; Segundo Porto, P. (UFERSA) ; Dantas Medeiros, H.A. (UFERSA) ; Teles Pinheiro, A.D. (UFERSA) ; Barbosa Rios, R. (UFERSA)
Resumo
O acetato de metila é um produto químico utilizado em uma grande variedade de sínteses e usualmente produzido pela esterificação do ácido acético com metanol. Estudos vêm apontando que a produção do acetato de metila pela carbonilação do dimetil éter com monóxido de carbono pode trazer vantagens, tais como: baixo custo de aquisição de um dos reagentes (CO), alto grau de pureza do produto e a redução do número de equipamentos. Dessa forma, o presente estudo tem como objetivos: definir as melhores condições de operação da planta e avaliar a viabilidade econômica da produção do acetato de metila via reação de carbonilação. A partir de uma análise econômica foram obtidos valores positivos para o Lucro Líquido Anual e para o VPL, o que indica a viabilidade econômica do processo estudado.
Palavras chaves
Acetado de Metila; Simulação de Processo; Avaliação Econômica
Introdução
O acetato de metila é utilizado como um intermediário em uma ampla variedade de sínteses, como por exemplo, no processo de preparação de nitratos de celulose e como matéria-prima na produção de ésteres e de anidrido acético (Cheunget al., 2007). Geralmente, o acetato de metila é produzido por esterificação do ácido acético com o metanol na presença de um catalisador ácido. Nesse processo tradicional, um reator e nove colunas de destilação são necessários para produzir acetato de metila com alta pureza. Uma vez que o metanol e a água formam misturas azeotrópicas binárias e terciárias nessa rota, a separação e a purificação do acetato de metila tornam-se bastante complicadas e de alto custo. A síntese de acetato de metila (MeOAc) também pode ocorrer a partir da reação exotérmica de carbonilação do dimetil éter (DME) com monóxido de carbono (CO), cuja reação global é dada pela Equação 1 (Diemer e Luyben, 2010). CH3OCH3 + CO ↔ CH3COOCH3 (1) Estudos de processos baseados na rota de carbonilação do DME ainda são escassos e merecem uma atenção maior, principalmente, por essa rota ser uma alternativa, em potencial, à rota de produção atual. Dessa forma, o presente artigo visa simular a produção do MeOAc pela rota de carbonilação, tomando como base o que foi proposto por Diemer e Luyben (2010), para se chegar em condições de operação ótimas, boas estimativas do tamanho dos equipamentos e uma avaliação econômica mais realista que possa atestar a viabilidade desse processo.
Material e métodos
A planta de produção do MeOAc pela rota de carbonilação do DME foi simulada, em estado estacionário, utilizando o software UniSim® Design Suite R430 da Honeywell (EUA). Inicialmente foram definidos os componentes químicos a serem utilizados na simulação da unidade industrial. A corrente de DME provém diretamente do processo de desidratação do metanol e contém água. Essa corrente de DME deve estar suficientemente seca, uma vez que o catalisador adotado é hidrofílico e a presença de água inibe a reação. Portanto, para a simulação, foi considerada a alimentação de DME como sendo pura. A corrente de CO foi considerada contendo 2% de hidrogênio e, por fim, foi incluído o MeOAc. O modelo termodinâmico adotado foi o UNIQUAC (Universal Quasi Chemical), uma vez que o processo contém correntes com misturas binárias líquido-vapor. Os coeficientes binários em falta no banco de dados do software foram estimados utilizando o método UNIFAC VLE (Universal Functional Activity Coefficient). O mecanismo da reação de carbonilação baseia-se na reação do DME, em fase gasosa, com o monóxido de carbono. A zeólita H- modernita foi sugerida como catalisador dessa reação em Diemer e Luyben (2010) e informações como a densidade da partícula (2500 kg/m³) foram incluídas na simulação. Para descrever esta reação, foram utilizados os dados cinéticos reportados em Cheunget al. (2007), bem como a equação da taxa de reação (Equação 2). r_carbon = k_carbon * (pCO / 1 + KW * pW) * (KDME * pDME / 1 + KDME * pDME) (2) onde pCO, pDME e pW são as pressões parciais do monóxido de carbono, do dimetil éter e da água em Pa, respectivamente; KDME e KW são as constantes de equilíbrio de adsorção do dimetil éter e da água em 1/Pa; e k_carbon é a constante cinética da taxa de reação em kmol/m³/s/Pa. Vale ressaltar que como foi considerada a alimentação de DME como sendo pura (sem a presença de água), foi assumido pW = 0 e a lei de velocidade pôde ser simplificada omitindo o termo (1 + KW * pW). O Investimento Total (ITOTAL) foi calculado a partir do somatório do Investimento de Capital Fixo (FCI), do Capital de Giro (WC). Foi considerado também o valor do terreno para compor o investimento total. O FCI por sua vez foi estimado a partir dos valores do ISBL, que é um parâmetro calculado a partir dos custos de cada equipamento da unidade industrial, como definido em Towler e Sinnot (2008). Os custos dos equipamentos foram calculados a partir das equações reportadas por Diemer e Luyben (2010) e das dimensões obtidas pela simulação deste trabalho. Obteve-se o Lucro Líquido Anual após Impostos (LL) com base em metodologia apresentada em Towler e Sinnot (2008) para o primeiro ano. O Valor Presente Líquido (VPL) foi calculado para o primeiro ano. Tomou-se como taxa de juros o valor de referência de 20%.
Resultado e discussão
A unidade de produção do MeOAc foi simulada tomando como referência a configuração da planta proposta
por Diemer e Luyben (2010), bem como as condições operacionais adotadas para as correntes dos
reagentes. A Figura 1 apresenta o Diagrama de Fluxo de Processo (PFD) da simulação gerada a partir das
alimentações: corrente 1 (DME puro, 318 K, 3242 kPa e 11520 kg/h) e corrente 2 (CO com 98 % de pureza,
321,3 K, 506,5 kPa e 7203 kg/h). A corrente 1 é aquecida até 374,15 K no refervedor E-100, promovendo a
vaporização total do dimetil éter, enquanto a corrente 2 é comprimida até 3242 kPa e misturada no
misturador estático MIX-100, juntamente com a corrente 12 proveniente do reciclo de monóxido de carbono
não reagido e pequenas frações de acetato de metila e hidrogênio. A corrente resultante (corrente 4) é,
então, misturada com a corrente de dimetil éter vaporizado (corrente 5) no misturador estático MIX-101,
gerando a corrente de vapor que irá alimentar o reator multitubular PFR-100, recheado com catalisador sólido
H-mordenite. O reator possui 1000 tubos de 0,05 m de diâmetro e 10,0 m de comprimento. O catalisador tem
uma densidade 2500 kg/m³ e o leito tem porosidade de 0,4. A reação de carbonilação no interior do reator é
exotérmica, havendo, então, a necessidade de remoção do calor gerado para manter a temperatura do reator
a 548,15 K. A corrente de vapor que sai do reator (corrente 7) é, então, arrefecida no condensador E-101 até
a temperatura de 273,15 K, ocorrendo a condensação parcial da mesma, e esta é alimentada a um vaso de
separação bifásica que opera a 3040 kPa e 273,15 K. O produto de fundo do vaso separador é rico em
acetato de metila a 99,19% e o vapor gerado no produto de topo é encaminhado para o reciclo, onde uma
pequena porção é purgada do sistema para remover parte do hidrogênio gerado na reação de carbonilação, e
a porção restante é comprimida no compressor K-101 até 3242 kPa para ser reciclada. Para obter as
melhores condições de operação para produzir o acetato de metila na unidade industrial, foram avaliados os
parâmetros que mostravam a melhor conversão do reator. Entre elas, foram analisados a temperatura do
reator, o comprimento dos tubos e a queda de pressão do mesmo. As Figuras 2 (a) e (b) mostram a
conversão do DME como função da temperatura do reator e do comprimento dos tubos, respectivamente.
Através da análise dos perfis gerados, os parâmetros obtidos para alcançar máxima conversão no reator e
menor custo foram: comprimento ideal de 10 m; temperatura de operação de 548,15 K; e queda de pressão
de 202,65 kPa para uma pressão de alimentação de 3242 kPa. Em relação a simulação proposta inicialmente
por Diemer e Luyben (2010), foi possível observar avanços a partir da simulação feita neste trabalho, como a
substituição da coluna de destilação por um vaso flash, redução do número de equipamentos e do gasto
energético total da planta, que era de 15.928 MW e foi para 13.058 MW. Com base nessa configuração final,
foi feita a avaliação econômica da unidade industrial.
Os resultados obtidos para o Custo de Aquisição de Equipamentos (Ce) foram: Refervedor (U$ 30.359,17),
Compressor K-100 (U$ 2.396,83), Reator PBR (U$ 631.593,27), Condensador (U$ 29.658,34), Vaso Fash (U$
225.207,84) e Compressor k-101 (U$ 579,91). Para o cálculo do Investimento Total de Instalação (ITOTAL), os
parâmetros obtidos foram: ISBL (U$ 3.679.181,46), OSBL (U$ 1.471.672,58), Custos de engenharia (Ceng)
(U$ 1.030.170,81), Custo de contingência (Ccont) (U$ 250.184,34), Capital de Giro (WC) (964.681,38),
totalizando U$ 9.791.100,14 de ITOTAL. Depreciação (D), Imposto de Renda (IR), ICMS, CONFINS e PIS
também foram considerados no fluxo de caixa. Assim, foram obtidos valores positivos tanto para o Lucro
Líquido Anual após Impostos (LL), quanto para o Valor Presente Líquido (VPL) para o primeiro ano, U$
61.703.700,85 e 67.859.256,57, respectivamente.
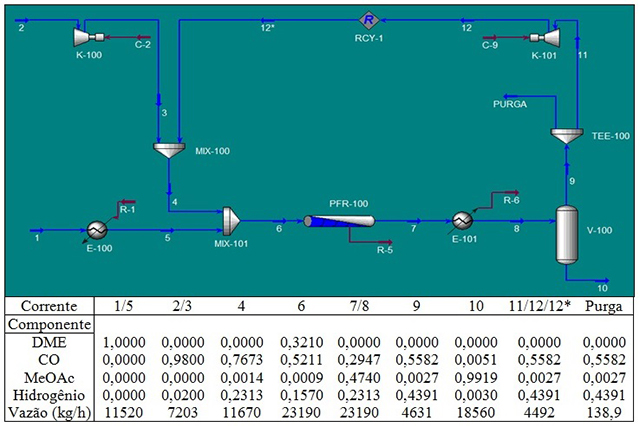
Figura 1 – Diagrama de Fluxo de Processo (PFD).
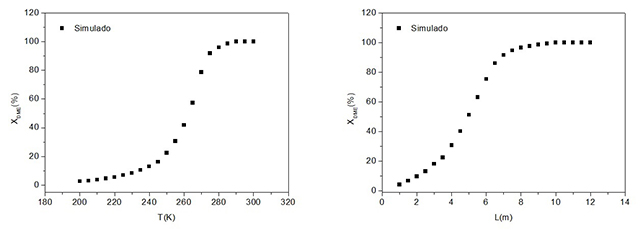
Figura 2 – Conversão de DME versus temperatura de operação do reator (a) e versus comprimento do reator (b).
Conclusões
A otimização de um processo alternativo proposto por Diemer e Luyben (2010) para produção do acetato de metila foi estudada neste trabalho. Os resultados obtidos para a unidade de produção do MeOAc foram satisfatórios frente a simulação original, uma vez que foi possível reduzir o número de equipamentos do processo e o gasto energético da planta, além de ter sido possível levantar as condições ótimas de operação do reator e ter se obtido um produto com alto grau de pureza. Valores positivos para o Lucro Líquido Anual e para o Valor Presente Líquido indicam que o processo de produção do MeOAc pela rota de carbonilação do DME é viável e merece ser mais estudado.
Agradecimentos
Os autores agradecem a Honeywell por ter concedido a licença do software UniSim® Design Suite R430 para o Curso de Engenharia Química da Universidade Federal Rural do Semi-Árido.
Referências
CHEUNG H, TANKE RS, TORRENCE G,Ullmann'sEncyclopediaof Industrial Chemistry: AceticAcid.Weinheim: Wiley, 2007.
DIEMER RB, LUYBEN WL. Design and Control of a Methyl Acetate Process Using Carbonylation of Dimethyl Ether. Ind. Eng. Chem. Res. J, v. 23p. 12224-12241, 2010.
TOWLER G, SINNOT R,Chemical Engineering Design: Principles, Practice and Economics of Plant and Process Design. Oxford: Elsevier, 2008.